We are located in Golden, Colorado and are active in the local lighting community helping new and existing users build and improve their displays. Meetings are held monthly in the Denver area on the 4th Saturday of the month except for in November and December when it’s the lighting season. Check out the Facebook group, Colorado Light Enthusiasts for more info.
From my earliest memories, the Christmas season always held a special place in my heart as I eagerly assisted my dad in setting up our modest Christmas light display. It may have been a simple outline on the eaves and railing along the upstairs balcony, but it filled the air with magic and excitement. As I grew older and started decorating my own house, I followed a similar path, gradually adding roof outlines, fences, and trees each year. Then, I stumbled upon a brilliantly synchronized light show, and that’s when I became captivated by the idea of taking my Christmas lights in that direction.
In 2015, I embarked on my journey with pixels, starting small by replacing my entire roof outline and programming a seven-minute loop of captivating patterns and color chases using Vixen 3 to accompany the static display. The following year, I switched to xLights and delved into creating fully synchronized light shows. Since then, my display has grown exponentially, with new key features introduced each year. When I sequence the lights, I immerse myself in the music, visualizing its melodies and transforming them into intricate designs in xLights. A sequence originates from just a few ideas, but as the process unfolds, new concepts emerge and develop into the sequence, revealing hidden layers and subtle nuances that can be discovered with each viewing. While it’s a time-consuming endeavor, the results are undeniably rewarding, with an average 3 1/2 minute song taking over 200-250 hours to sequence, some even exceeding 300 hours.
As my passion for Christmas lighting grew, I found myself in need of innovative mounting solutions and custom parts, which is where 3D printing became an invaluable asset. The versatility of 3D printing in the Christmas light hobby is vast, but it’s important to note that 3D printing itself is a hobby with its own learning curve. Creating your own designs or modifying existing ones to suit your specific needs requires time and experience, often gained through trial and error. Choosing the right printer and deciding between prebuilt options or kits can be daunting. Additionally, understanding the intricacies of print settings, such as layering, wall thickness, infill percentage, temperature, retraction, and more, takes patience and experimentation. Dealing with challenges like failed prints, bed adhesion issues, stringing, under extrusion, over extrusion, warping, and clogs is inevitable along the way. After navigating through these complexities, I became proficient in 3D printing and began offering my services to those who preferred a finished part without the hassle of owning a printer. While learning 3D printing can be a rewarding endeavor, many newcomers to the hobby lack the time and patience to tackle these complexities while also building their light display. That’s why we provide an extensive selection of ready-to-use mounts and clips, eliminating the need for individuals to purchase a printer and independently figure everything out. For those who do own a printer and want to tackle a printing project, we offer STL files for nearly all our designs, allowing you to create the parts yourself. If you have a unique idea that we haven’t covered, we’re more than happy to collaborate with you and design a custom solution tailored specifically to your requirements.
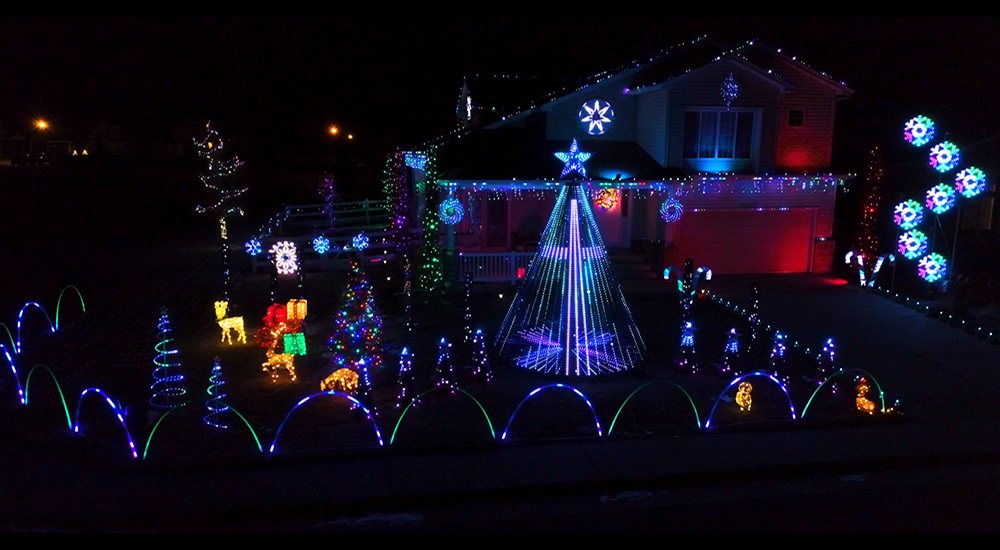